Inventory Shrinkage: What is it and How Do You Reduce it?
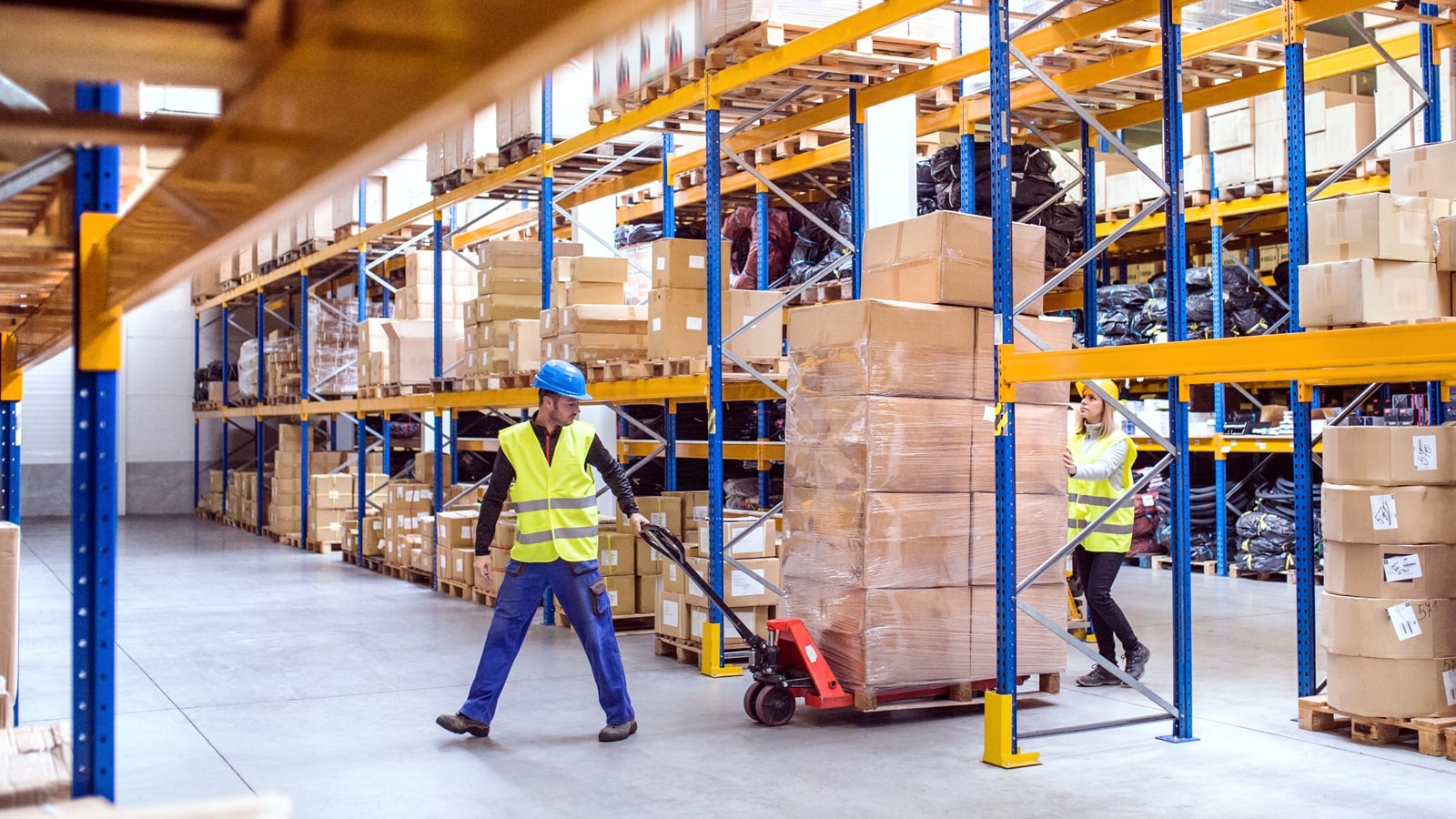
For companies that distribute food products, inventory is the lifeblood of the business. Being in the grocery/food business, you know the importance of inventory management.
In this blog, we’re going to look at one of the most common issues in the grocery sector when it comes to inventory – shrinkage.
What is inventory shrinkage, and why is it a problem?
Inventory shrinkage is stock that exists on a business’ inventory records but is lost, damaged, or has gone past the expiration date. This can be costly for organizations, particularly those with slim margins, as any shrinkage means money off the balance sheet and spoiled products that they cannot sell.
As a general example, a grocer might have $400,000 of fresh produce in its warehouse, according to its inventory management system. But during a physical inventory count, it’s found that only $375,000 worth of products can be accounted for. That would account for 6.25% of shrinkage and cost the business $25,000. In addition to financial implications, that percentage of shrink could also mean delayed order fulfillment and the potential of putting contracts in jeopardy.
Grocers and food distributors operate on slim profit margins - anywhere between 1% to 3% - so it only takes one pallet of fresh produce to go missing for those margins to get squeezed.
The problem is compounded for grocery businesses because produce will be written off in a few days due to being out of code. In many industries, shrinkage can be reversed by finding missing items, even many months later. But, in the just-in-time world of groceries and food products, misplacing a pallet for just a day or two can mean significant funds down the drain.
What is an acceptable level of inventory shrinkage?
In an ideal world, the answer would be zero, but some inventory shrink is inevitable. Inventory can be misplaced either by accident or on purpose, even with the most sophisticated warehouse management systems. Human error is the leading cause of inventory being misplaced, and in the grocery and food business, a missing pallet is likely to go out of date and be written off. Labels can come unstuck, and pallets put in the wrong place – the key is keeping it to an absolute minimum and catching mistakes early and often.
Perceived wisdom has always been that inventory shrink under 1% is acceptable, but the 2020 National Retail Survey found inventory shrinkage accounted for an average of 1.62% of retailers’ bottom lines. That number was even more significant in the grocery sector, with U.S. grocers reporting average shrinkage of 3.1% of revenues pre-pandemic, according to the Food Industry Association.
Not all shrink is down to warehousing errors though; employee and consumer theft are also common causes. But, just as grocers spend billions of dollars on security systems for their stores and facilities, they should also invest in warehouse technology to cut unnecessary losses.
How can I reduce inventory shrink in my warehouse?
Traditionally, businesses have tried to cut inventory shrinkage with people. It’s not unusual to see warehouse inventory teams looking for lost inventory with binoculars to get a view of pallets some 40 feet above the ground. But that is an inefficient and expensive way to recover missing inventory. Some businesses send workers to great heights to get a closer view, but that method is becoming increasingly avoided because of safety concerns.
Increasingly, it’s become more cost-effective and efficient to use automation to help keep inventory shrink to a minimum in warehouses and distribution centers. Technology has advanced significantly in recent years, and should be considered as part of your approach to cutting inventory shrinkage and recovering misplaced items.
In the middle of a serious labor shortage, utilizing technology also allows you to automate tedious tasks that would previously have taken days or even weeks. By automating inventory tracking, you can negate the effects of the rising personnel costs and your employees can work on tasks that deliver more value to the business.
Increase inventory accuracy with automation
Automated inventory tracking has been designed to make warehousing and inventory operations more efficient. It allows you to count at increased rates while your valued employees can focus on higher-value tasks. And by counting more often, you’re likely going to have a more accurate picture of current inventory in your warehouse. Mistakes will be found sooner, and shrinkage will be reduced dramatically.
An automated inventory control system using drones in your warehouse can count 900 pallets per hour and can scan inventory way more often than would be feasible using manual inventory control team members.
Transform your warehouse.
No infrastructure changes necessary
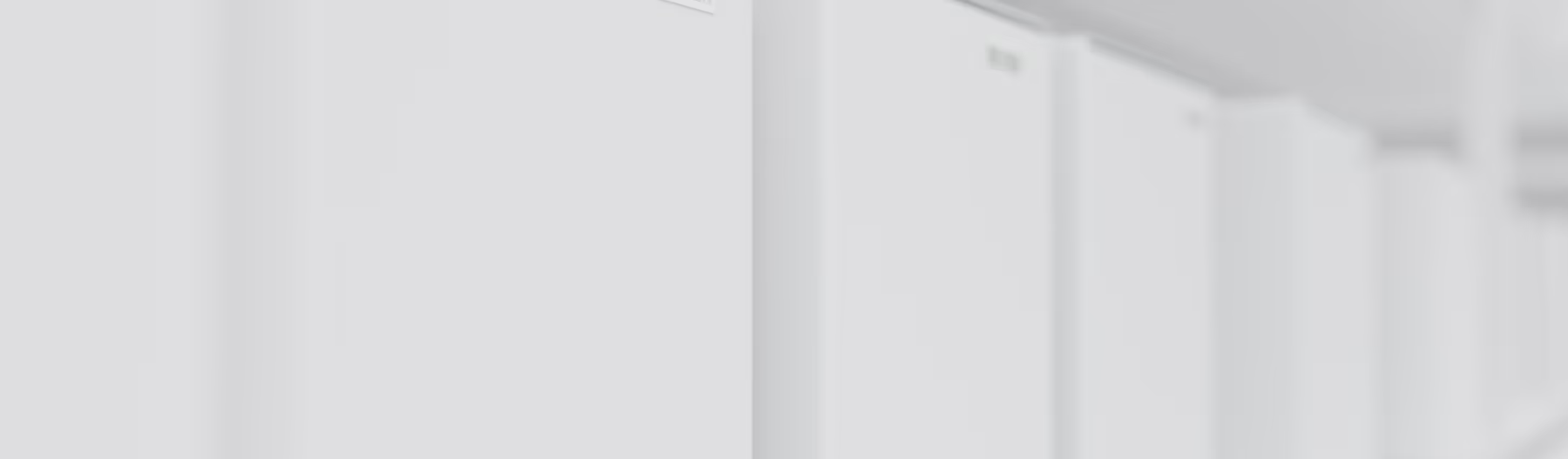